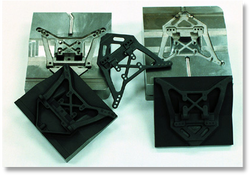
The procedure of urethane casting may be implemented for rapid prototype for quite a while to produce high-quality parts monetarily. Several plastic injection molding companies implemented this procedure to help make prototypes of parts by injection molding. In past times, many customers do not understand that such a process provides a great method to create creation parts. Even so, with the massive numbers of buyers who chosen this process, it is widespread in quite a few industries.
Logic behind why they decide on urethane casting
First, they acquired reduced upfront investment intended for tooling.. The money necessary for tooling for creating cast urethane parts is much less costly compared with the tooling for an injection-molded component. Moreover, another option for clients can take advantage is the cost for amortizing tools on the piece cost.
Second, you may be eased to produce modifications when it comes to urethane casting. This technique and the low-cost tooling involved help it become less complicated and reasonable to make most required corrections.
Third, this process will offer fast transformation. Parts constructed from cast urethane can be done fast, so organizations can provide it thus to their clients in one to two weeks’ time. On the contrary,parts produced from injection molding are done in between eight to ten weeks.
Lastly, this course of action has apperance that can certainly last including those parts produced from injection molding. Cast urethane parts could be customized its paint, color or even texture. This implies that parts made out of this process will continue to look great, even if they become ruined or scraped.
Bear in mind it is essential to understand that this action has a much quicker longevity compared with injection molding. Whilst the latter will make thousands of parts, a cast urethane mold could make partial quantity of parts in line with the design as well as material needed of the part. Nonetheless, for constructing products that few parts each month, it will take a very long time to establish the return of investment of trading to injection molding.
Additionally, cast urethane parts charge more each and every piece compared with injected-molded parts. The root of this is that urethane casting is a more labor-intensive method than its counterpart is. In spite of the higher price of urethane casting per part, individuals still preferred this action because they can save a lot more in total costs by preventing the bigger upfront charges of tooling. As an outcome, buyers can be able to put the money they saved to different expenses required.
Logic behind why they decide on urethane casting
First, they acquired reduced upfront investment intended for tooling.. The money necessary for tooling for creating cast urethane parts is much less costly compared with the tooling for an injection-molded component. Moreover, another option for clients can take advantage is the cost for amortizing tools on the piece cost.
Second, you may be eased to produce modifications when it comes to urethane casting. This technique and the low-cost tooling involved help it become less complicated and reasonable to make most required corrections.
Third, this process will offer fast transformation. Parts constructed from cast urethane can be done fast, so organizations can provide it thus to their clients in one to two weeks’ time. On the contrary,parts produced from injection molding are done in between eight to ten weeks.
Lastly, this course of action has apperance that can certainly last including those parts produced from injection molding. Cast urethane parts could be customized its paint, color or even texture. This implies that parts made out of this process will continue to look great, even if they become ruined or scraped.
Bear in mind it is essential to understand that this action has a much quicker longevity compared with injection molding. Whilst the latter will make thousands of parts, a cast urethane mold could make partial quantity of parts in line with the design as well as material needed of the part. Nonetheless, for constructing products that few parts each month, it will take a very long time to establish the return of investment of trading to injection molding.
Additionally, cast urethane parts charge more each and every piece compared with injected-molded parts. The root of this is that urethane casting is a more labor-intensive method than its counterpart is. In spite of the higher price of urethane casting per part, individuals still preferred this action because they can save a lot more in total costs by preventing the bigger upfront charges of tooling. As an outcome, buyers can be able to put the money they saved to different expenses required.